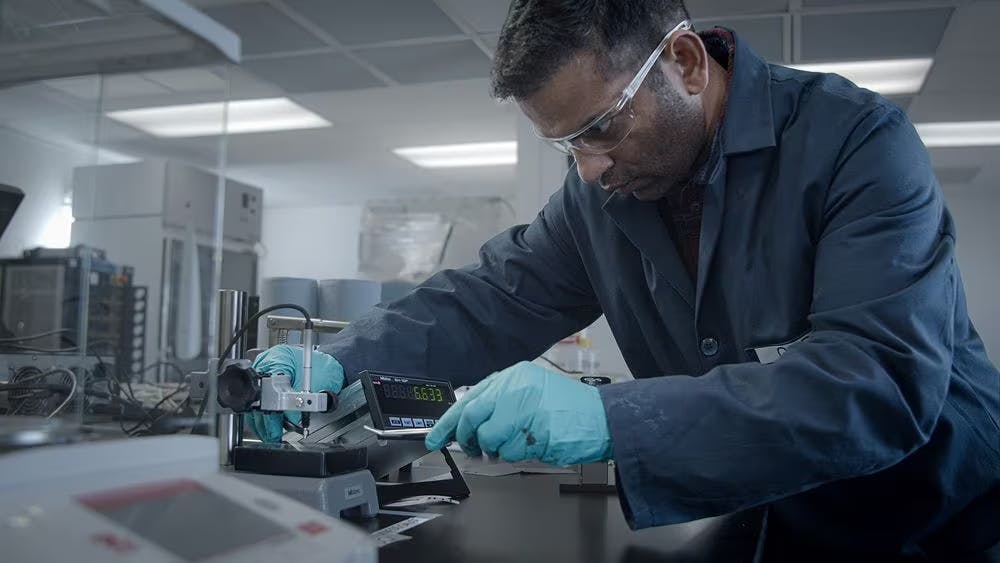
Toyota Teams Up for Recycled EV Battery Production
The push toward electric vehicles (EVs) is accelerating rapidly, driven by the need to reduce our reliance on fossil fuels and mitigate the environmental impact of traditional gasoline-powered vehicles. However, as the momentum for EV adoption continues to build, so does the demand for the raw materials required to produce the batteries that power these vehicles. To maintain this momentum and ensure that the transition to EVs is sustainable, it’s crucial to address two significant challenges: sourcing the materials needed for battery production and finding environmentally responsible ways to manage used batteries.
One of the most promising solutions to these challenges is battery recycling. Not only does recycling prevent aged-out batteries from ending up in landfills, but it also plays a key role in meeting the growing demand for battery materials. Redwood Materials, a leader in the battery recycling industry, is at the forefront of this effort, making significant strides in domestic battery production using recycled materials.
The Importance of Cathode Active Materials in Battery Production
At the heart of every battery lies the cathode, a crucial component that defines the battery’s composition and contains the bulk of the rare metals used in its construction. In lithium-ion batteries, which are commonly used in EVs, the cathode is essential for the movement of lithium ions between the cathode and the anode during charging and discharging. This process is vital for the battery’s functionality, making the cathode a key element in battery design.
The composition of the cathode determines the types and quantities of metals required for its production. These metals include lithium, cobalt, and nickel, all of which are essential but often challenging to source. For instance, cobalt is primarily sourced from the Democratic Republic of the Congo, a region plagued by child labor and human rights abuses. Nickel, on the other hand, is largely mined in Indonesia, where its extraction has had devastating effects on the local environment. Beyond the ethical and environmental concerns associated with mining these materials, there is also the substantial cost and carbon footprint of shipping them around the world.
Redwood Materials: Pioneering Sustainable Battery Production
Redwood Materials is addressing these challenges by establishing a domestic source for cathode materials. The company is currently constructing a Cathode Active Material building at its facility in Nevada, marking a significant step forward in its mission to produce batteries from recycled materials. Redwood’s approach not only reduces the reliance on conflict-ridden and environmentally damaging sources of battery materials but also strengthens the EV battery ecosystem within the United States.
Redwood’s goal is ambitious: to produce cathode materials that are 90% recycled, with a composition of 30% recycled nickel, 30% recycled lithium, and 100% recycled cobalt. The process involves breaking down used batteries, extracting valuable elements, and refining them into a substance known as "black mass." This metal-rich material is then processed to pull out specific elements needed for battery production.
The construction of Redwood’s cathode production building is the first of four planned facilities. Once completed, these buildings are expected to produce a total of 100 gigawatt-hours (GWh) of cathode materials annually, enough to power approximately 1.3 million EVs. The first building alone is projected to produce 20 GWh of cathode materials each year.
Toyota’s Role in the Future of Recycled Batteries
Redwood Materials has already secured significant partnerships to support its vision of sustainable battery production. The company has signed contracts with both Panasonic and Toyota to supply them with cathode materials produced at its Nevada facility. Panasonic plans to use these materials at its De Soto, Kansas battery factory, while Toyota will integrate them into its American battery factory, which is currently under construction in North Carolina. Both factories are expected to begin production in 2025, with Redwood Materials set to start deliveries of cathode active materials to Panasonic by the end of 2024.
Toyota’s involvement in this initiative is particularly noteworthy. As one of the world’s leading automakers, Toyota’s commitment to using recycled materials in its battery production demonstrates the company’s dedication to sustainability. By incorporating Redwood’s recycled cathode materials into its battery manufacturing process, Toyota is taking a significant step toward reducing the environmental impact of its EVs and contributing to a more sustainable future for the automotive industry.
The Road Ahead: Sustainable EV Production
As the demand for EVs continues to rise, the need for sustainable and ethical battery production becomes increasingly critical. Redwood Materials’ efforts to create a domestic supply of recycled cathode materials represent a significant advancement in this area, offering a solution to the challenges of sourcing rare metals and managing used batteries. With major players like Toyota on board, the future of EV battery production is looking more sustainable than ever.
By focusing on recycling and reusing materials, companies like Redwood Materials and Toyota are helping to ensure that the transition to electric vehicles is not only feasible but also environmentally responsible. As we move forward, the lessons learned from these efforts will be crucial in shaping the future of transportation and reducing our reliance on fossil fuels.